Vor mehr als 70 Jahren legten die Eltern von Dr. Volker Dreve den Grundstein für das Unternehmen, das nun als einer der Weltmarktführer Otoplastiken und Know-How in über 100 Länder liefert.
„Meine Eltern waren absolute Pioniere auf dem Gebiet der Otoplastiken, als sie hier 1949 ihren Zwei-Personen-Betrieb gegründet haben“, sagt Dr. Volker Dreve. Er hat nicht nur das Erbe der Firma angetreten, sondern setzt auch den Pioniergeist seiner Eltern weiter um. „Wir haben jetzt kürzlich unser komplettes Otoplastik-Labor erneuert, aber eigentlich befinden wir uns in einem permanenten Prozess der Erneuerung. Vieles, was in ein paar Jahren auf dem Weltmarkt Standard wird, haben wir hier in Unna entwickelt.“
Auf dem Gebiet der Otoplastiken geht es im Moment schlicht nicht moderner, als bei Dreve an der Max-Plack-Straße in Unna. Volldigitales Arbeiten und das Ergebnis kommt aus dem 3D-Drucker und passt so haargenau ins Ohr, dass der Träger überhaupt nicht merkt, dass er eine Hörhilfe trägt. Aber langsam: Was genau ist ein Otoplastiklabor?
Axel Kohlmann leitet das neue Labor und erklärt: „Wir stellen zum Beispiel die Verbindung der technischen Hörhilfe mit dem menschlichen Körper her.“ Fangen wir beim Menschen an und befassen uns zunächst mit Hörgeräten. Wer merkt, dass er schlecht hört, geht zum Hals-Nasen-Ohren-Arzt und macht einen Hörtest. Bestätigt sich die Hörschwäche, stellt der Arzt eine Verordnung aus - wichtig für die Krankenkasse - und es geht zum Akustiker.
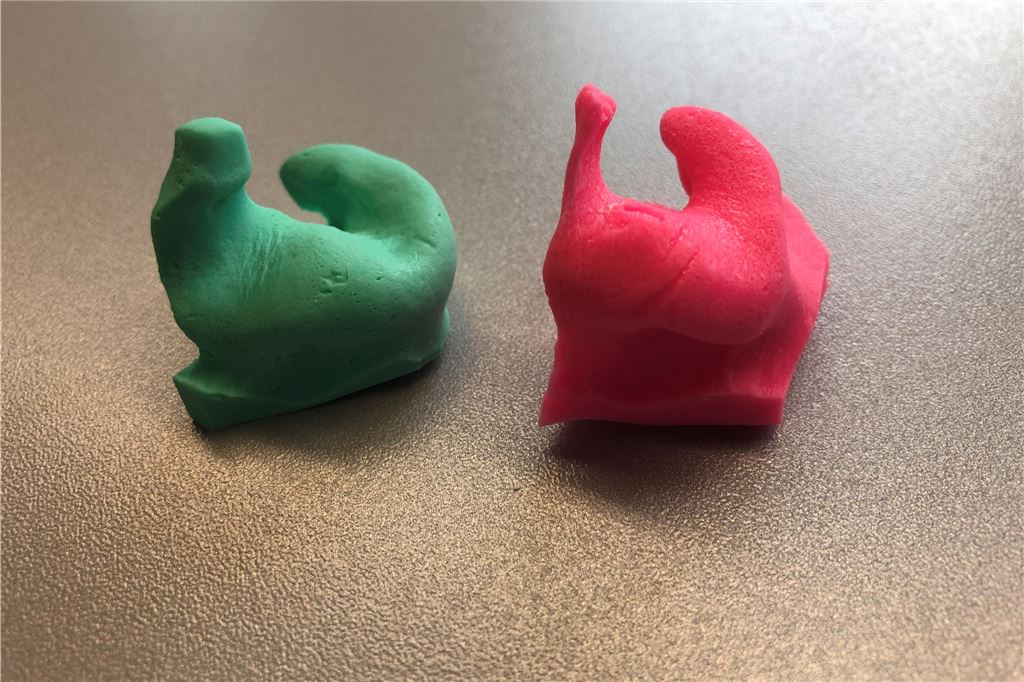
Diese Ohrabformungen werden dann im Labor gescannt und für den 3D-Drucker digitalisiert. © Christoph Schmidt
„Der Akustiker fertigt dann eine Ohrabformung an“, sagt Laborleiter Kohlmann und zeigt auf zwei bunte Klumpen, die auf dem Tisch vor ihm liegen. „Diese Abformungen sind sozusagen die Schablonen der Ohren mit denen wir arbeiten, diese bekommen wir dann zugeschickt und scannen sie dreidimensional ein, sodass wir das am Computer bearbeiten können.“
Das Bearbeiten am Computer ist wichtig, damit der 3D-Drucker hinterher auch weiß, welche Form er drucken muss. Bleiben wir beim Beispiel des Hörgeräts. Anhand der Ohrabformung ist nun eine dreidimensionale Computergrafik entstanden, die nun an den 3D-Drucker gesendet wird, der aus dem Kunststoff „FotoTec“ das passende Ohrstück formt.
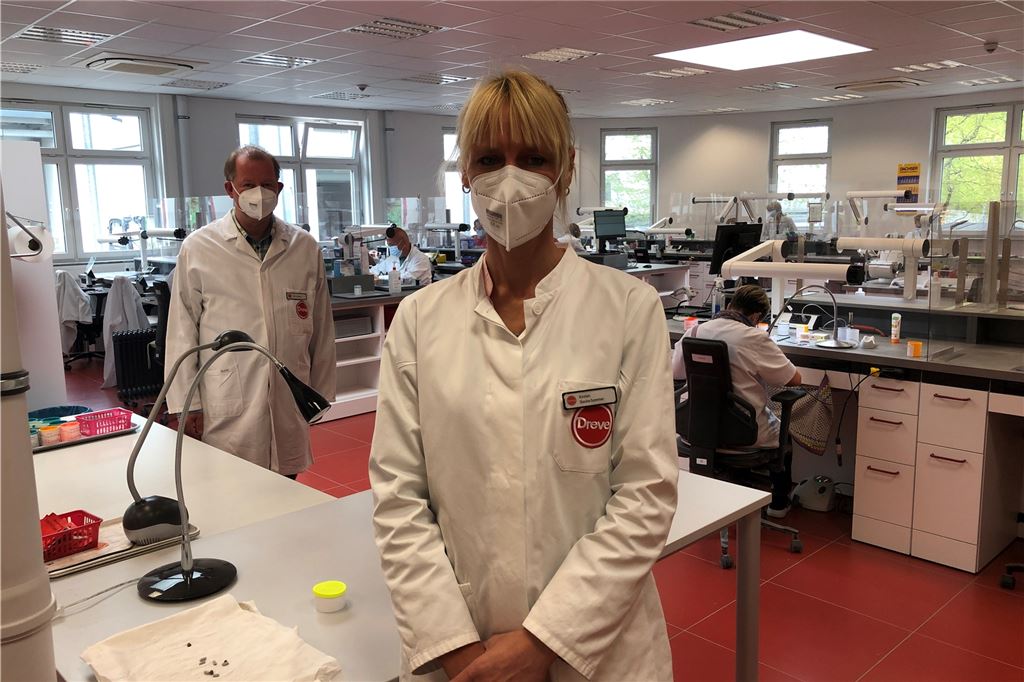
Kirsten Stacke-Sommer und Axel Kohlmann haben im neuen Otoplastiklabor bei Dreve das Sagen. © Christoph Schmidt
2000 Stück schafft das Labor jeden Tag und bei der Modernisierung hat sogar ein bisschen die Pandemie in die Karten gespielt, wie Dr. Dreve verrät. „Wir haben da ganz schnell geschaltet. Weil durch Corona so viele unserer Mitarbeiter im Homeoffice sind, konnten wir für die Umbau- und Modernisierungsarbeiten die freien Räume nutzen. Eigentlich war geplant, ein Ausweichsquartier auf dem Parkplatz zu bauen - das konnten wir uns so sparen.“
Je nachdem, welches Material für die Otoplastiken verwendet wird, ändert sich auch die Methode der Verarbeitung. Bleiben wir zunächst bei dem nun geformten Stück eines Hörgeräts (FotoTec), das in den Gehörgang eingeführt wird. Aus dem 3D-Drucker kommt es nicht einzeln, sondern auf einer Platte mit dutzenden anderen. Die Otoplastik wird separiert und von dem kleinen Sockel, der für das Druckverfahren nötig ist, abgetrennt. Das geschieht mit einer feinen Fräse, und in Handarbeit wird die Oberfläche bearbeitet, entgratet und geglättet.
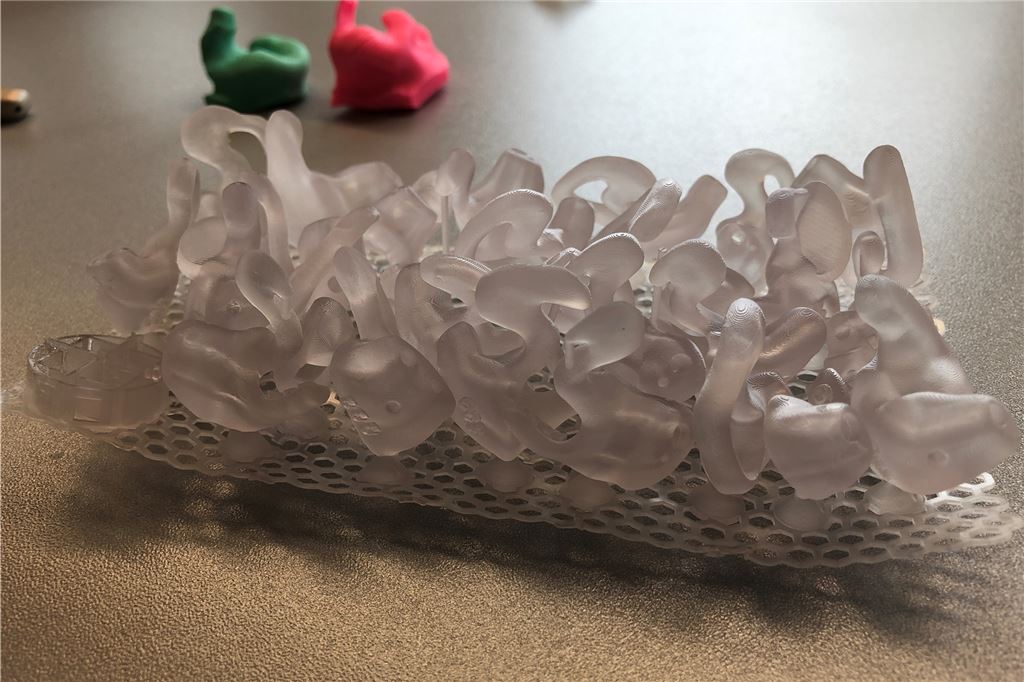
So sehen die Rohlinge aus, wenn sie aus dem 3D-Drucker kommen, jetzt beginnt die Handarbeit. © Christoph Schmidt
Dann wird die Otoplastik noch mit dem Laser graviert und erhält eine Schutzbeschichtung zur einfacheren Reinigung und einen Nylonfaden, damit man die Otoplastik leichter wieder aus dem Ohr herausbekommt. Jetzt kann man die Otoplastik an das technische Bauteil des Hörgeräts anschließen und fertig. Dadurch, dass jede Otoplastik ihre individuelle Seriennummer hat, ist jedes Teil exakt einem Kunden zuzuordnen und kann im Verlustfall auch leicht nachbestellt werden.
Otoplastiken sind aber nicht nur Teile von Hörgeräten, bei Dreve wird noch wesentlich mehr fürs Ohr hergestellt. Zum Beispiel individueller Gehörschutz für Menschen, die in sehr lauten Umgebungen arbeiten, wie aus Metall verarbeitenden Betrieben, und auch für Menschen, die einen hohen Anspruch an die Klangqualität haben, nämlich Musiker. „Hierbei ist es wichtig, dass der Schall linear gedämmt wird, sonst verfälscht sich der Klang und nur bestimmte Frequenzen werden herausgefiltert“, erklärt Laborleiter Kohlmann.
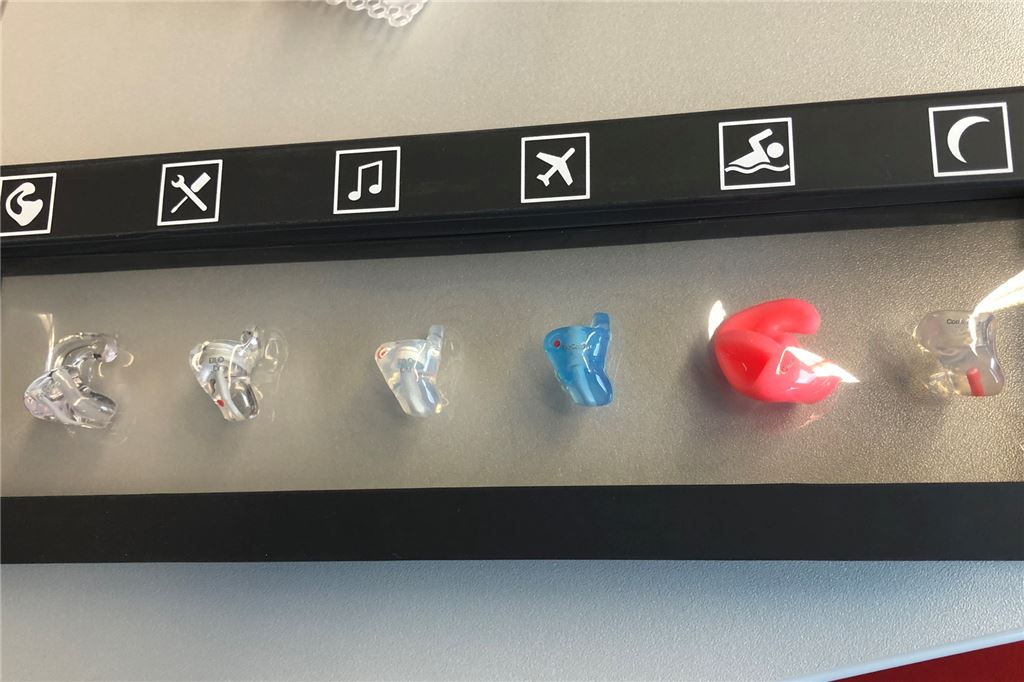
Die Otoplastiken sind vielseitig einsetzbar, als Lärmschutz für die Nacht, gegen Wasser beim Schwimmen, als Druckausgleich für Piloten und Vielflieger, für Musiker, den Arbeitsplatz und natürlich als Teil eines Hörgeräts. © Christoph Schmidt
Das ist aber noch lange nicht alles: Es gibt spezielle Otoplastiken für Piloten oder Vielflieger, die den Druckausgleich beim Starten und Landen erleichtern, für Schwimmer, damit beim Training oder Wettkampf kein Wasser in den Gehörgang eindringen kann und auch im Radsport kommen die Otoplastiken zum Einsatz, wenn etwa über den sogenannten „Knopf im Ohr“ Radprofis mit ihrem Team über Funk in Kontakt bleiben.
Egal um was es geht, Materialien, Verarbeitungstechnik oder Software, eines der größten Zentren für Otoplastiken weltweit steht in Unna.
1982 in Dortmund geboren. Abi in Holzwickede, Journalistik-Studium wieder in Dortmund. Seit 2013 Redakteur beim Hellweger Anzeiger. Freut sich über die spannende Herausforderung, den Wandel eines Traditionsverlags hin zu einem modernen, familiengeführten Multimedia-Unternehmen zu begleiten.
