Erst der Angriffskrieg Russlands. Jetzt die Abkehr der USA von Europa. Zwei sogenannte Zeitenwenden, aber ein Resultat: Mehr Arbeit, vor allem für die Rüstungsindustrie. Problem: Fehlender Platz, weil Hallenkapazitäten nicht ausreichend sind. Die Firma „Sabura international“ an der Herbert-Wehner-Straße 27 im Technopark in Kamen hat dafür eine Lösung. Mobile Raumsysteme – oder mit einfachen Worten: Faltbare Hallen.
Die auf wenigen Quadratmetern zusammengeschobenen Konstruktionen aus Stahl und schwer entflammbaren Folien vergrößern sich auf Knopfdruck auf voluminöse Hallen, die überall in Windeseile aufgestellt werden können. „Unsere längsten Hallen sind einhundert Meter lang – da passt ein ganzer Zug rein“, sagt Firmengründer Udo Schwabe (69), der das ungewöhnliche Unternehmen mit seinem Sohn Christoph Schwabe (40) leitet.
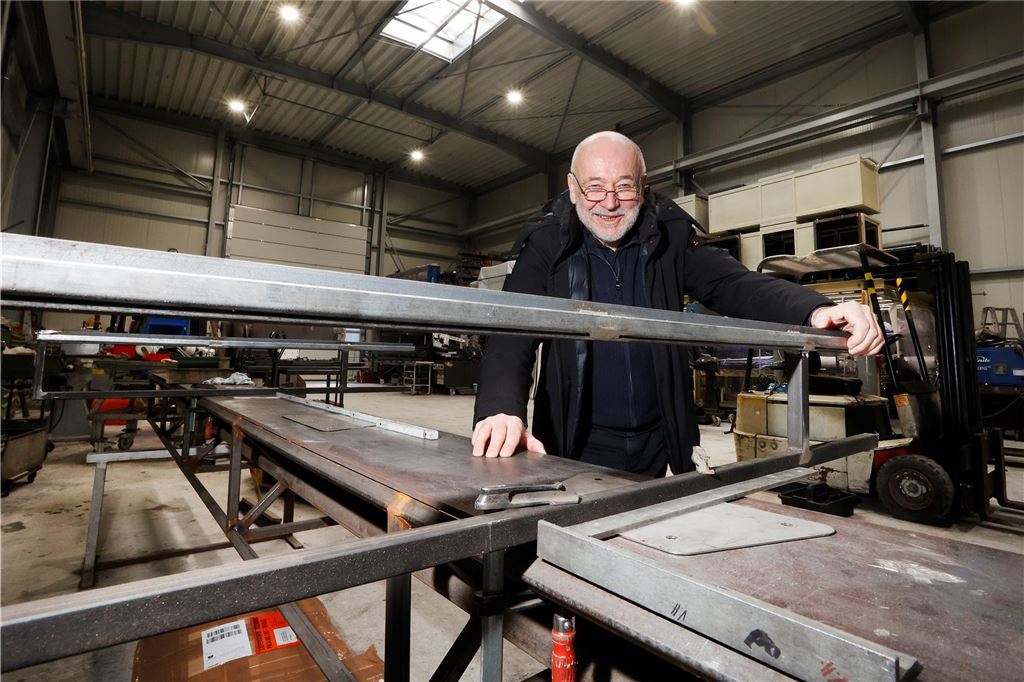
Rüstungsunternehmen geben Falthallen in Auftrag
Seitdem die Schwabes mit ihrer Erfindung auf dem Markt sind, werden sie mit Aufträgen überrannt. Waren es zunächst vor allem Eisenbahnunternehmen aus Deutschland, Österreich und der Schweiz, die für Fertigung und Wartung zusätzliche Hallen-Kapazitäten benötigten, klopfen nunmehr immer öfter Rüstungsunternehmen an, damit Panzer, Panzerhaubitzen und sogar Raketen aufgearbeitet, lackiert und getarnt werden können.
„Unsere Auftragsbücher sind gefüllt bis ins nächste Jahr“, sagt Schwabe. „Und wir nehmen nur so viele Aufträge an, wie wir auch abarbeiten können.“ Rheinmetall, Diehl Defence und Krauss-Maffei zählen jetzt zu den Kunden. Einzelheiten dazu gibt es öffentlich nicht. Wegen vertraglicher Verschwiegenheitsklauseln.
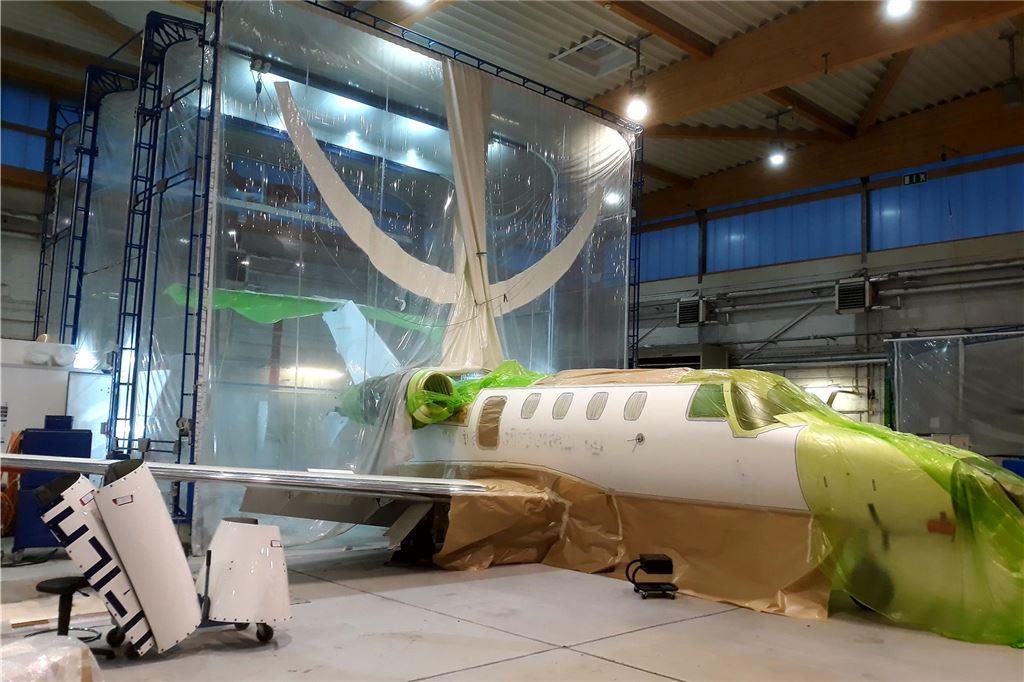
Erfindung einst am Wohnzimmertisch entwickelt
Dass ein mittelständisches Unternehmen wie Sabura bei Unternehmen wie Airbus, Lufthansa, Cessna, Bombardier, Siemens, dem französischen Eisenbahnbauer Alstom oder der Glacier Express AG im schweizerischen Andernmatt so gefragt ist, liegt daran, dass Udo und Christoph Schwabe auf eine eigene Erfindung zurückgreifen können. „Die ist konkurrenzlos und gibt es nirgendwo anders“, sagt Udo Schwabe, der nicht nur Elektroingenieur ist, sondern als Tüftler, Entwickler und Erfinder auch eine Art Daniel Düsentrieb. Er muss lachen, wenn er daran denkt, dass vor manchem Vertragsabschluss noch eine europaweite Ausschreibung notwendig ist. „Dann sage ich dem Kunden: Kannst du machen. Ist aber sinnlos.“
Im Jahr 2007 erfanden die Schwabes das „faltbare Raumsystem“ über die Weihnachtstage mit einem Modell aus Holz und Papier auf dem Wohnzimmertisch. Von Jahr zu Jahr wuchs das Interesse. Etwa ein halbes Dutzend der raffinierten Falthallen verlässt das Kamener Werk pro Jahr. „Die Tendenz ist steigend“, so Schwabe.
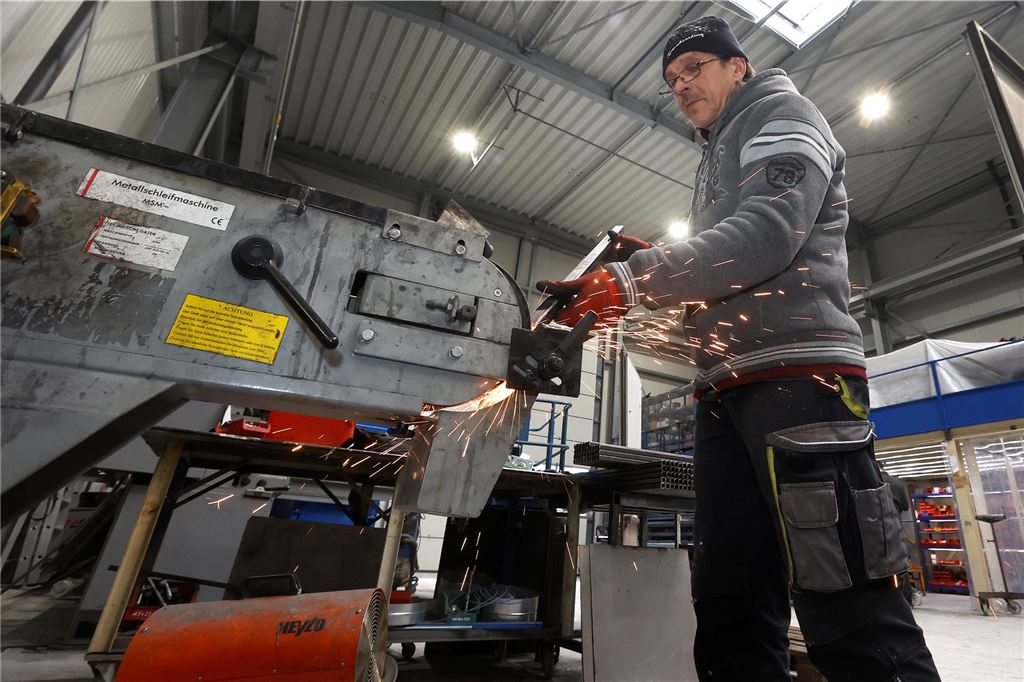
Besonderes Raumklima auf Knopfdruck
Das liegt auch daran, dass es immer mehr Anwendungsmöglichkeiten gibt für die Sabura-Hallen, in denen durch die eingebaute Technik besondere klimatische Bedingungen hergestellt werden können. Fürs Schleifen. Fürs Lackieren. Für Reparaturen.
Und neuerdings auch fürs Verkleben von Scheiben. „Scheiben in Zügen und Straßenbahnen werden nicht mehr geschraubt, sondern verklebt“, erläutert Schwabe. „Damit sie bei einer Vollbremsung nicht aus dem Rahmen fliegen, benötigt es beim Kleben bestimmte Bedingungen in Sachen Luftfeuchtigkeit, Temperatur und Trocknungszeit. In zu großen Hallen geht das nicht.“ Mit der Sabura-Halle schon. Denn die kann auch in einer großen Werkshalle aufgefaltet werden. Eine Halle in der Halle.
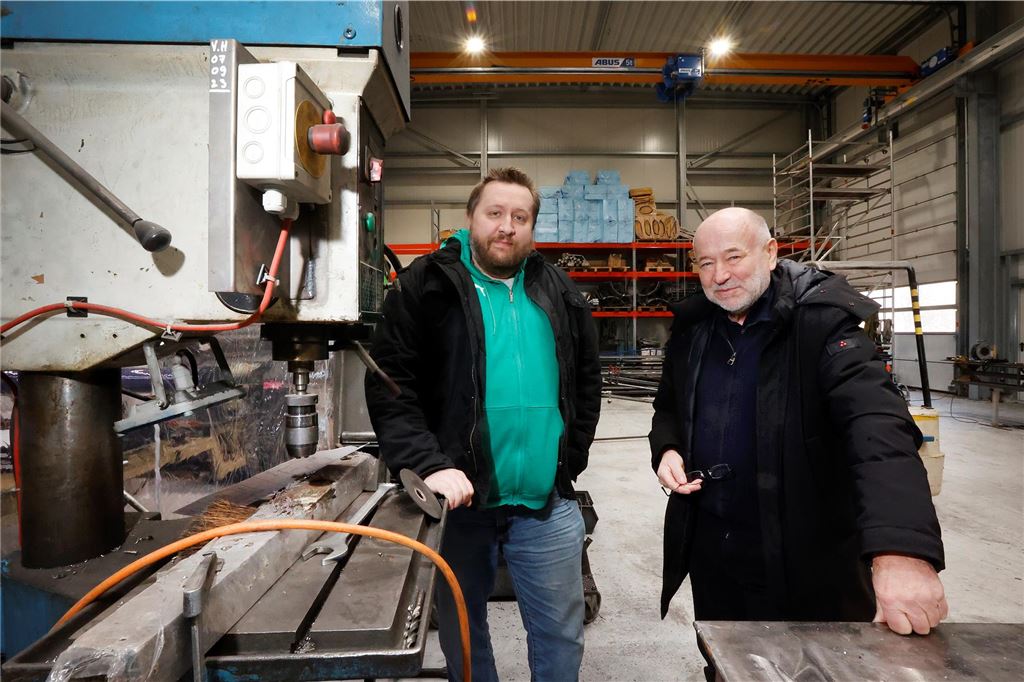
Zweiter Standort im Kosovo vor dem Aufbau
Zu viel Bürokratie und langsame Prozesse in den Behörden. Das bundesweit von Unternehmen angeprangerte Phänomen spürt die Firma aus dem Technopark ebenso. „Wir müssten als Firma eigentlich schon viel größer sein“, so Schwabe. Doch die bürokratischen Hürden seien oft so groß und vielfach, dass Wachstum erschwert würde. „Das Unternehmen hat sich hervorragend entwickelt. Genau so, wie wir es erwartet haben. Was wir nicht erwarten konnten, ist, dass es in Deutschland so schwer ist, zu wachsen.“
Deshalb baut Schwabe gerade einen zweiten Standort in Pristina, der Hauptstadt der Republik Kosovo, auf. Dort werden bereits jetzt Elemente der Stahlkonstruktion geschweißt und dann mit 40-Tonnern nach Kamen gefahren. Trotz der Entfernung von 2100 Kilometern beschleunigt das die Abläufe. „Der Lkw fährt anderthalb Tage – dann ist er hier.“